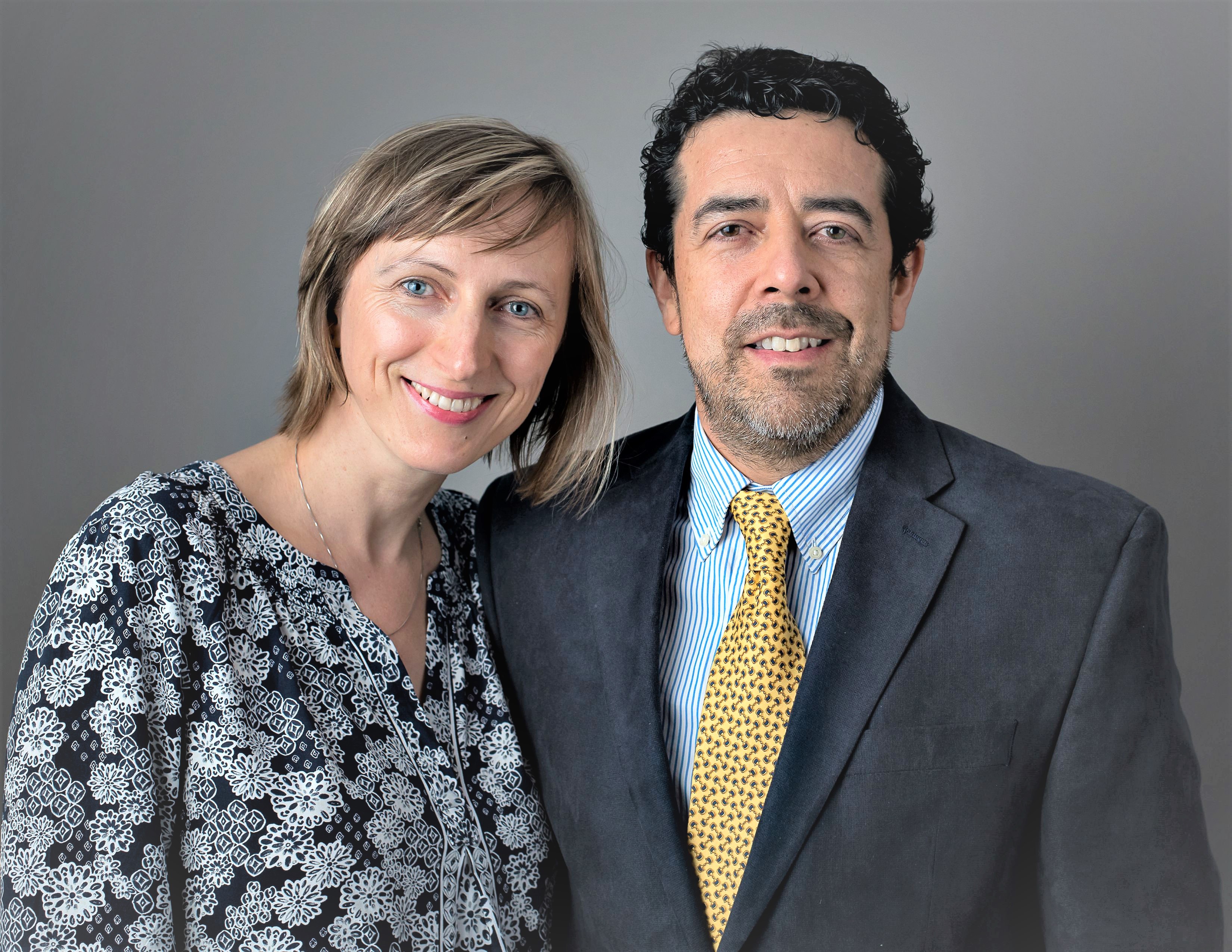
Justyna Mazur
Since 2003, Justyna has been working as Director of Quality Assurance and Quality Control at OhmPharma Homeopathic Pharmacy, which she runs with her husband, Robert Melo.
JUSTYNA MAZUR
CURRICULUM VITAE
EDUCATIONAL BACKGROUND
Maria Curie-Sklodowska University, Lublin, Poland, Bachelor of Science, Graduation June 2001 Major: Chemistry and Physics.
Minor: Analytical Chemistry, Grade Point Average: 3.91
Maria Curie-Sklodowska University, Lublin, Poland, Master of Science, Graduation May 2003 Major: Chemistry.
Minor: Colloid Chemistry and Radiochemistry, Grade Point Average: 4.05
EDUCATIONAL EXPERIENCE
Practices in chemical and physical laboratory (analytical, organic, physical and radio chemistry) Research into adsorption and zeta potential on the oxides
Establishing and coordinating various organizations
Research and computer support to professors and staff
PROFESSIONAL EXPERIENCE
2002 September – October: Internship as a chemistry teacher assistant at High School, Lublin, Poland.
2003 June – Present:
Director of Quality Assurance and Quality Control
Multiple courses in cGMP pharmaceutical manufacturing and homeopathic pharmacy.
Overseeing preparation and manufacturing process.
Overseeing regulatory compliance documents with HPUS, FDA cGMP (CFR 210 & 211), ICH and WHO guidelines.
Overseeing quality control laboratory (revision and approval testing methods, SOP’s and forms).
Principal Responsibilities:
1. Develops and maintains Quality Systems in support of pharmaceutical cGMP requirements in a lean manufacturing environment.
2. Develops and coordinates GMP training program for company personnel to include documentation and evolution of effectiveness.
3. Creates, reviews, and executes any remediation plans, updates validation and qualification documentation for FDA compliace requirements.
4. Directs internal auditing, internal corrective action requests, customer corrective action requests, qualification of suppliers, and quality initiatives. Prepares audit reports.
5. Coordinates company department meetings to review quality concerns and help identify areas for process improvement.
6. Identifies opportunities for improvement through review and analysis of quality indicators, data analysis, internal audits, and customer satisfaction surveys.
7. Creates, reviews and maintains company procedures, records, forms, and other documentation in accordance with quality and regulatory requirements and guidelines. Oversees document control activities. Oversees the flow and development of the QMS documentation within the organization.
8. Investigates customer complaints, and approves reports. Implements Corrective and Preventive Action (CAPA) plans related to complaints. Submits reports to customers, and coordinates product return or recall if applicable.
9. Investigates, reviews and approves reports related to nonconforming materials or products, and any returned products.
10. Oversees creating the Change Control and Deviation records. Assures that all affected departments are trained according to approved changes.
11. Assures that all QMS reports for CAPA, Investigations, Non-conformance, Complaints, Change Control, Document Change Control, Risk Assessments, etc. are closed in a timely manner as per internal procedures.
12. Directs company quality programs; develops manufacturing specifications and implements quality systems for manufacturing processes. Oversees In Process Quality Assurance manufacturing activities from storage of raw materials to the final product dispatch. Oversees ERP activities related to the manufacturing process.
13. Supports new product introduction process to ensure compliance with quality systems and successful integration of new products into operations.
14. Monitor performance of the company quality system through corrective and preventive action; collect relevant data and produce statistical/trending reports.
15. Assists in the revision of completed batch records, environmental monitoring data, laboratory records, and other ancillary data for product release.
16. Oversee the Quality Control department to ensure all testing is conducted per GLP guidelines.
17. Reviews and approves Out of Specifications investigation reports.
18. Reviews stability testing program and evaluates shelf life of the products.
19. Provides QA support and evaluates validation activities using industry standards, company policies, and federal regulations.